[ad_1]
Engineers and technicians have filmed test-fires of bullets, missiles, rockets, artillery shells and aircraft since the early days of the proving ground. Slow motion movies have fascinated many people for decades. The advanced tracking and imaging technology used to make them provides a window into a previously unseen world. slowly disperse from the expansion of .
process The technology behind these images and movies also has serious uses. Images and videos from testing are used to carefully validate performance and improve designs. Since the advent of digital cameras in the 2000s, there has been much consolidation in the area of high-speed imaging. However, there are still a few companies that provide equipment used by professional tracking and photo-based metrology technicians to collect data about projectiles.
‘)
}
// –>
Disney days
Much high-speed tracking technology has its roots in entertainment. Photo-Sonics is a global supplier of the equipment used to track projectiles. The US company can trace its origins back to 1925, when it worked as machine shop for Walt Disney, supplying cameras and equipment for animation photography.
By the late 1940s Photo-Sonics had shifted its focus to supplying high-speed instrumentation cameras to the Department of Defense (DOD) and test ranges, benefiting from the DoD’s emphasis on the development of missiles. The company’s first mechanical tracking systems were developed in the 1960s and were manually operated. Photo-Sonics still works with the entertainment industry, but the advent of digital video and photography means the company focuses on supplying the optical tracking systems and gimbals used in weapons testing.
Simon Harris is managing director of Photo-Sonics in the UK. As well as the tracking systems, the company supplies flight test instrumentation and telemetry equipment from Safran. The tracking systems are a
long-term strategic capability that most countries with armed forces possess. The use and maintenance of the systems is complex and requires highly trained engineers and technicians.
“The primary application of optical tracking systems is to provide time, space and positioning information [TSPI] and attitude data for airborne objects such as missiles, rockets and artillery. This data is used to determine the performance of the test item, such as speed, acceleration, and miss-distance, as well as engineering sequential data such as the deployment of control surfaces or the position of the thrust vectoring nozzles” says Harris.
The sensor and optical payload of the systems include a combination of high speed visible, SWIR, MWIR cameras and both fixed focal length and metric zoom lenses. The company can provide fixed focal length lenses of between 3000 to 5000mm.
The systems are equipped with high resolution optical encoders to record azimuth, elevation and time down to the microsecond to determine the precise position of a target up to 500 times per second. The data from two or more systems is used to triangulate a 3D position of the target. “They include a very accurate bearing for elevation and azimuth, so there is no accuracy run off,” says Harris.
The gimbals use very powerful, direct drive DC torque motors to track high-speed targets including hyper-velocity targets traveling over 2000m/sec or over 4,400mph (7000km/h). “Tracking a missile at that speed requires a tremendous amount of velocity and acceleration to slew the six sensors and lenses and the weight of the rotating portion of the gimbal which weighs over 3000 lbs. The azimuth motor in our large Fly-Out system provides 1500 foot-pounds of torque or the equivalent of three V8 engines,” Harris says.
Automatic tracking of the target is accomplished through real-time image based tracking algorithms. “The video tracker detects movement against the background by comparing pixel grey levels between the object and background. After the positive detection of a target, the video tracker drives the servos of the gimbal tracking the target through its trajectory, from launch until impact.” says Harris.
Photo-Sonics is halfway through a contract to supply 90 tracking systems to the US DOD as part of a range modernization program. “There is innovation going into the latest systems, including automated star calibration to improve accuracy, self-surveying capabilities for ease of use, multi-gate video trackers for tracking multiple target and multi-station processing and control systems used to generate real-time TSPI data and provides a 2D and 3D visualization,” Harris says.
Some mounts have radars fitted to them, but these systems are heavy, harder to use and inherit the weaknesses that radar has.
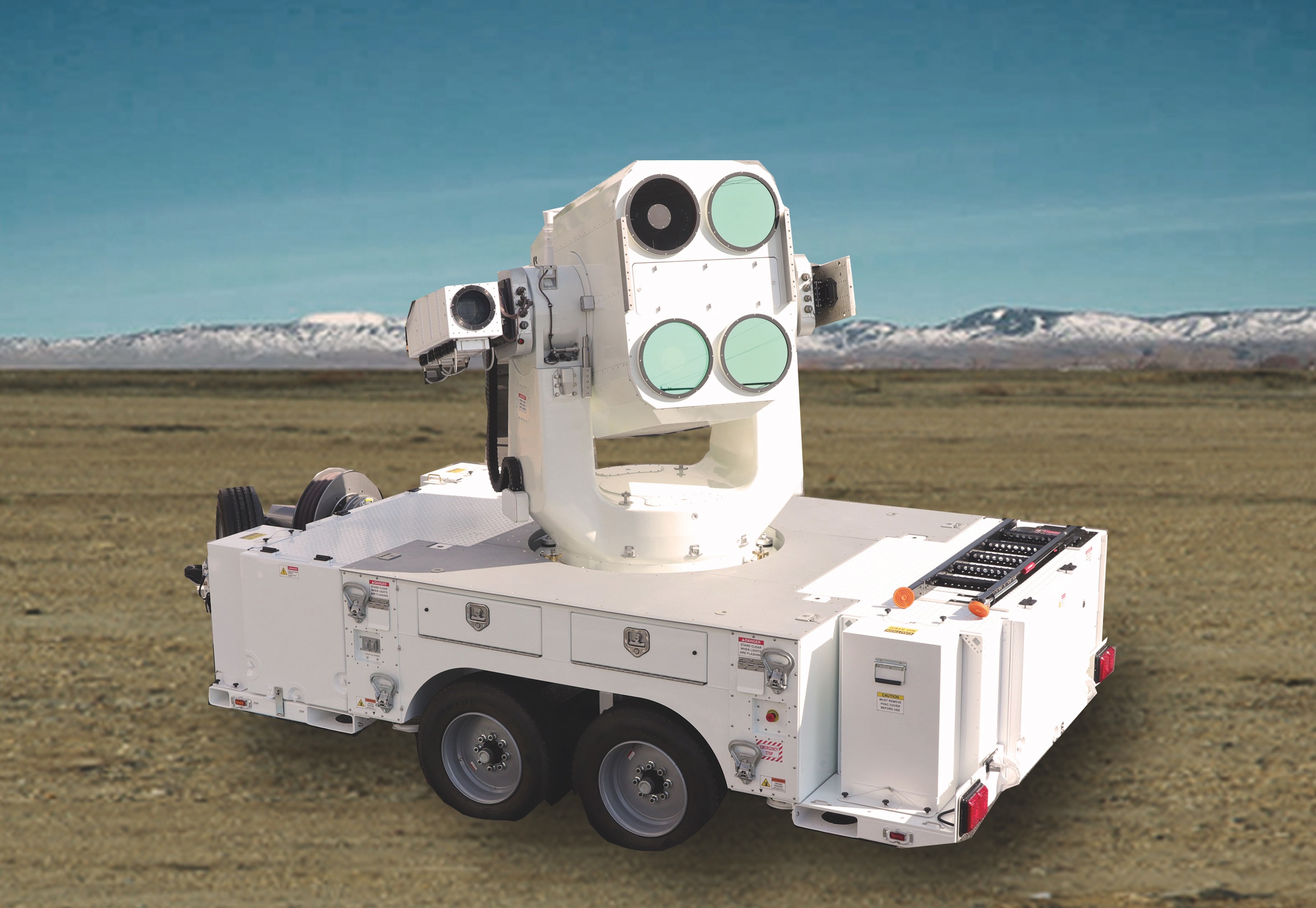
This imaging and tracking system with side-mounted radar can track from sidereal speeds of up to 120°/second (Image: Photo-Sonics)
A billion frames per second
UK-based Specialised Imaging is another of the companies serving the niche of projectile tracking for high-speed imaging. Similarly to Photo-Sonics, it’s Tracker 2 system uses a system of mirrors in front of a camera that moves at the same speed as the projectile to tracking its flight. The device is normally used to track ballistics on test ranges. Tracker 2 can be integrated with any high-speed camera.
The company also supplies cameras, such as its SIM range, for capturing images of extremely high-speed events. Its equipment captures 32 images – at a maximum rate of a billion frames per second. That’s only nanoseconds, but as Wai Chan, managing director of Specialised Imaging says, a lot can happen in nanoseconds, especially if you are recording at many millions of frames per second.
“If an OEM wants to see a bird strike on an engine, they will use high-speed video cameras that give seconds of recording time,” says Chan. “But if they want to see an electrical strike on a wing, that happens in a couple of microseconds. You need a high-speed camera for that. Most research of that type is now done at universities.
“Our SIM cameras are used to look at stress on materials, electrical discharge and injection/combustion performance. From looking at nanoparticles in medicines to hypersonics research with gas guns. The number of applications they have been used for is endless.”
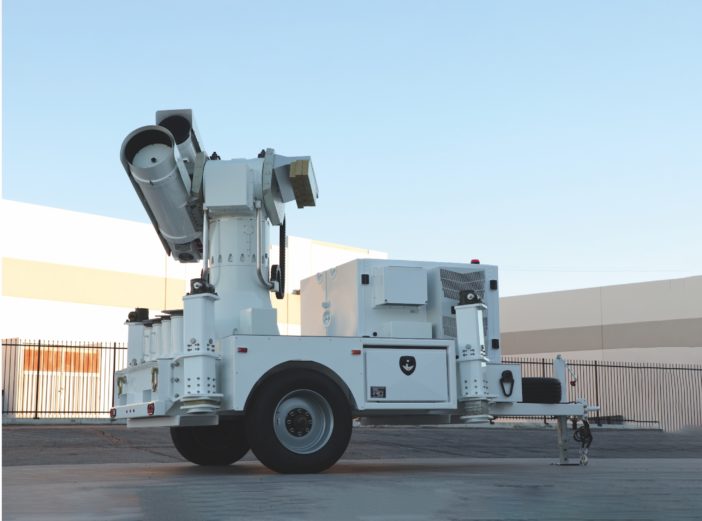
The Mini Sextant tracking mount has four sensor stations to enable the collection of Time Space Position Information (Image: Photo-Sonics)
Specialised Imaging’s cameras are used in materials R&D and testing in techniques such as digital image correlation. As well as weapons testing and aviation companies, the company also supplies cameras to the space sector. For example, Specialized Imaging’s cameras have been used to assess the damage caused by micrometeoroids striking the shielding of space vehicles. NASA White Sands Test Facility uses its cameras, and they helped verify one of the last space shuttle launches after problems had been identified with debris hitting the spacecraft’s undercarriage.
Trigger time
One of the most challenging aspects of high-speed imaging is ensuring you start recording at the right time, Chan explains: “The triggering part is always the most difficult. We have several triggering solutions and always work with customers to get the timing right. We do this by understanding their experiment, the triggering device and visualizing this using timing diagrams. But it is never going to be perfect, there is always going to be some jitter.
“With the trajectory tracker, the really clever thing is to take the triggers that are coming in, work out a new velocity and instantly reprogram the scan rate to correct the scan. All our cameras have a built in delay generator and multiple triggering configurations so that we can simplify the synchronization with the event. Unfortunately with the SIM cameras we can’t go backwards in time, only forwards. Our Kirana camera, which is our next generation of ultra high-speed video camera can capture frames before the trigger, which comes in useful for example when looking at micro-droplet icing on wings.”
The other challenge for ultra high-speed imaging is ensuring that there is sufficient light. Chan explains: “You can never have enough light. When you’re outdoors with the tracker its worse. You’re relying on the Sun and you need to capture the image at a fast enough rate.”
According to Chan the requirement from customers is for faster cameras – more frames per second to analyze, for example, a cavitating particle if it is expanding or exploding. The particle could be as small as 30 microns and moving at 50m/sec. At 40 or 50 times magnification the particle is moving at 500m/sec. This requires extremely high-speed cameras to capture the movement. Another area that demands ever faster image capture speeds is laser or light research.
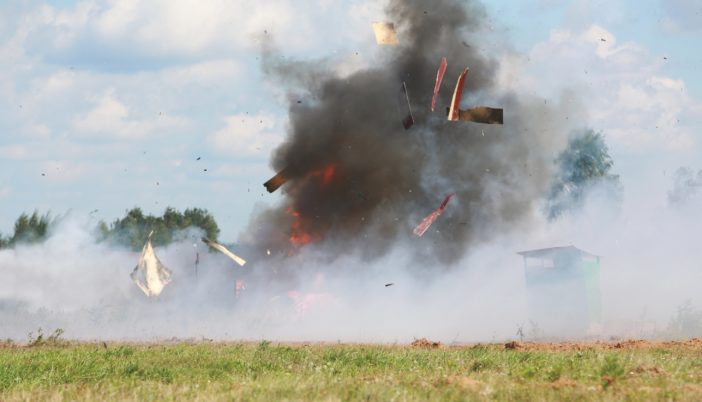
High-speed tracking and camera technology can be used to film and analyze the impact of ballistics
(Image: andreysafonov- stock.adobe.com)
This type of R&D drives fundamental research into the silicon used in CMOS (complementary metal oxide semiconductor) sensors. High-speed cameras use image intensifiers and CCDs (charged couple devices). The end goal, adds Chan is to replicate the image intensifier with just pure silicon.
He says, “Our latest camera sensor runs at seven million frames per second – we are trying to go faster even than that. The challenge is to get the silicon to go fast enough to transfer the image without generating so much heat it melts the sensor.
“There is no end point to how fast people want to go. The faster the better.”
Above this level, engineers would usually choose to use a streak camera. These instruments measure the variation in a pulse of light’s intensity over a time period. They are used to measure the pulse duration of ultrafast laser systems and for applications such as time-resolved spectroscopy and LIDAR. Optical companies may work together to supply combinations of different types of cameras to meet a customers requirements – streak cameras and high-speed cameras or high-speed video cameras.
“Working from a common viewpoint, one optical point, is better than two viewpoints because it makes correlation so much easier,” says Chan. “Our camera will give the fundamental process and the high-speed video will give them the overall process.”
Video tracking for enthusiasts
Video tracking for enthusiasts Several video tracking solutions are now on the market that analyze images. Several devices also exist that link cameras with tripods capable of movement. These consumer-orientated products are becoming popular with, for example, aviation enthusiasts filming aircraft. Tracking technology also crosses over with the tracking of balls in sports such as golf and baseball, and in the entertainment industry, although the systems used in these sectors would not be suitable for use at test ranges.
[ad_2]
Source link